The Making of a Module: How do we do what we do?
One of the most common queries we get here at Noise Eng regards how we create modules. Today on the blog, we’ll talk a bit about that process, and how things tend to happen here at NE.
First, a bit about Noise Eng. People are often surprised to learn that it’s just two of us. This is not uncommon: a lot of Eurorack companies are pretty small. NE started as a hobby project for Stephen when we were both in wildly different careers. It only really became a full-time endeavor for the two of us in 2017. I mention this because it frames our workflow and how we approach modules and our general company ethos.
Step 1. Conception of an Idea
We get ideas for modules from a lot of places. Sometimes friends or customers come to us and ask about something. The Manis Iteritas, for example, was an idea that friends Matt Lange and Anthony Baldino suggested. Sometimes we just see a hole in the market or in our cases that we wish we could fill. Some modules are simple utilities that we think need to be in the lineup (a mixer, for example. Everyone makes a mixer, but if we want to release cases, we should have our own, right?).
We typically have a stack of about 100 ideas on paper. I say stack because we put them on notecards and periodically revisit these...so yes, there is an actual stack of notecards in NE HQ with module dreams.
Many of these will never be made, some will be combined with other ideas into a better idea, but we never really have a lack of ideas to draw from. What we have on paper sometimes is pretty true to the module we produce. Other times, it bears minimal resemblance. The hardest part for us is choosing which ones move on to...
Step 2. Design
Once we decide to try out an idea, it moves into design. We start on paper: what should the module do? What controls should it have? How many knobs and jacks will we need? We draw it out and try to find ways to maximize control with as simple an interface as possible. This cuts down on hp, but also on cost.
Once we have a basic idea of what we want on the front panel, for oscillators and some effects, Stephen uses our Noise Engineering Rapid Development Software (NERDS) to produce a quick mockup in software to see if it’s worth following through with design. This step can save us a huge amount of time and money in development costs. If it passes this test, we start designing the circuitry. This may fall to either of us. After the schematic is set, we layout the front panel and route the PCB. Then it’s time for…
Step 3. Prototype
When we’re ready to test it out, we send the design off to our manufacturer. They order the PCBs in their next batch and then put it all together and send it back. If there is firmware to be written, Stephen does that.

Step 4. Test
Once we have the module working, we start putting it through its motions. This may be simple with something like the Mullet, or may require a lot ot test across different users / uses. We test basic function and simple things like current draw at our work benches (only partly an excuse to buy fun toys like oscilloscopes), and then we put them in our cases.

We have lots of friends locally who we also get a lot of feedback from. We take all of their thoughts and...
Step 5. Revise
Sometimes the revisions we make are minor enough that all we need to change are a few resistor values (which Kris can do at the bench), but other times we redesign the whole thing from scratch. When the changes become big enough, we send the PCB off for another round of prototyping.
Each prototype needs more test, and may need a firmware update, so revisions are costly. They are also time consuming: a hardware revision can take a few months from the time we finish the PCB to when we have a new version in hand. While we don’t expect to get most modules perfect on the first attempt (even if the only change is a slight difference in the panel layout), it's important to think through as much as possible each revision and only do a revision when we're ready.
The number of revisions varies wildly. Some of our older modules when Stephen was first learning to do this had a huge number of revisions. Some still do when we have module in search of an identity. We like to think we’ve gotten better at this though, and hope that we have streamlined this a little bit.
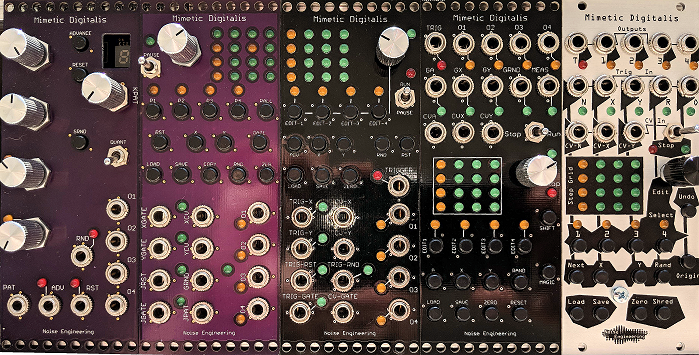
Step 6. Production
When we finally are confident that we have the final design, we get a build quote. This is a moment of truth: we’ve gotten to a product we think may be compelling in a size we think may be compelling, but only if the price makes sense to our customers. If the stars align, our manufacturer goes into production.
One side not here is that we’ve learned that we have to be willing to abandon an idea if one of these components isn’t there: the features, the size, the price. If all of those are not compelling, people won’t buy it. There’s a box hidden away in NE HQ of old, non-functional prototypes that never made it to production for (at least) one of these reasons. One day, they will make it to e-cycle or an art project, but for now they collect dust.
Step 7. Prepare for Release
This is when things get real. Modules are built, panels are made. Modules go to the photographer for professional-quality images. Manuals get written now that features are finalized. Final hardware gets tested and retested, firmware gets polished, and we measure things like current draw and voltage responses once again. Preorder information is out to retailers and on social media. We work with the awesome Patrick O’Brien to create videos and start creating some of our own. And so much more. It’s a busy week before launch, and we couldn’t do it without the help of our manufacturer, who also fulfills all the orders for us, freeing us up to spend more time on module development!
Step 8. Release into the wild!
That’s where you, dear user, come in. Speaking of which, have you seen the new Muta Jovis and Soleo Vero shipping next week? Quad mute and what’s this? A 4hp patch-through tuner for THREE oscillators? Be sure to pick them up!